A delaminação em PCB pode levar a problemas significativos de desempenho, especialmente em projetos rígidos-flexíveis, onde materiais rígidos e flexíveis são combinados. Compreender como evitar a delaminação é crucial para garantir a longevidade e a confiabilidade desses conjuntos complexos. Este artigo explorará dicas práticas para prevenir a delaminação de PCB, com foco na laminação de PCB, compatibilidade de materiais e parâmetros de usinagem otimizados.
Compreendendo a delaminação de PCB
A delaminação ocorre quando as camadas de uma PCB se separam devido a vários fatores, incluindo estresse térmico, absorção de umidade e tensão mecânica. Em PCBs rígidos e flexíveis, o desafio é maior devido às diferentes propriedades dos materiais rígidos e flexíveis. Portanto, garantir a compatibilidade entre estes materiais é o primeiro passo para prevenir a delaminação.
Garanta a compatibilidade do material PCB
A escolha dos materiais é fundamental para prevenir a delaminação. Ao projetar uma PCB rígida-flexível, é essencial selecionar materiais que tenham coeficientes de expansão térmica semelhantes. Esta compatibilidade minimiza o estresse durante o ciclo térmico, o que pode levar à delaminação. Além disso, considere o adesivo utilizado no processo de laminação. Adesivos de alta qualidade projetados especificamente para aplicações rígidas e flexíveis podem aumentar significativamente a resistência da união entre as camadas.
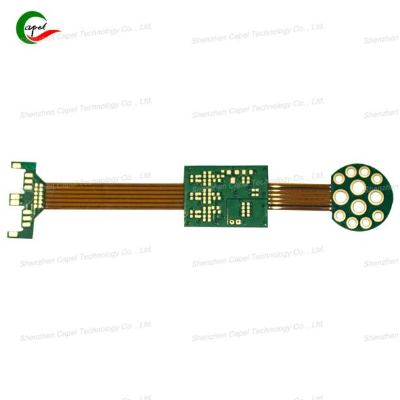
Processo de laminação de PCB
O processo de laminação é uma etapa crucial na fabricação de PCB. A laminação adequada garante que as camadas adiram bem umas às outras, reduzindo o risco de delaminação. Aqui estão algumas dicas práticas para uma laminação eficaz de PCB:
Controle de temperatura e pressão: Certifique-se de que o processo de laminação seja conduzido na temperatura e pressão corretas. Uma temperatura muito alta pode degradar os materiais, enquanto uma pressão insuficiente pode levar a uma má adesão.
Laminação a Vácuo: Usar vácuo durante o processo de laminação pode ajudar a eliminar bolhas de ar que podem causar pontos fracos na ligação. Esta técnica garante uma pressão mais uniforme nas camadas do PCB.
Tempo de cura: Aguarde um tempo de cura adequado para que o adesivo adira adequadamente. Apressar este processo pode levar a uma adesão incompleta, aumentando o risco de delaminação.
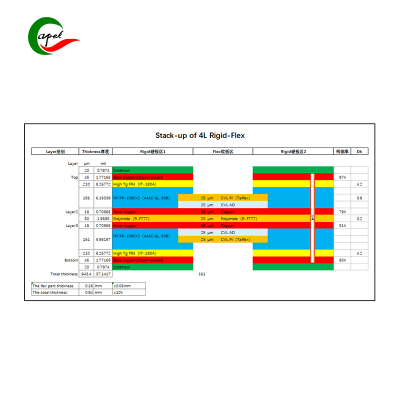
Parâmetros de usinagem de PCB Rigid-Flex otimizados
Os parâmetros de usinagem desempenham um papel significativo na integridade dos PCBs rígidos e flexíveis. Aqui estão algumas dicas de usinagem otimizadas para evitar delaminação:
Técnicas de Perfuração: Use brocas e velocidades adequadas para minimizar a geração de calor durante o processo de perfuração. O calor excessivo pode enfraquecer a ligação adesiva e levar à delaminação.
Roteamento e Corte: Ao rotear ou cortar a PCB, certifique-se de que as ferramentas estejam afiadas e bem conservadas. Ferramentas cegas podem causar pressão e calor excessivos, comprometendo a integridade das camadas.
Tratamento de Borda: Trate adequadamente as bordas da PCB após a usinagem. Isto pode envolver alisar ou selar as bordas para evitar a entrada de umidade, o que pode contribuir para a delaminação ao longo do tempo.
Dicas práticas para prevenir a delaminação de PCB
Além das estratégias acima, considere as seguintes dicas práticas:
Controle ambiental: Armazene os PCBs em um ambiente controlado para evitar a absorção de umidade. A umidade pode enfraquecer a ligação adesiva e causar delaminação.
Testes Regulares: Implementar testes regulares de PCBs em busca de sinais de delaminação durante o processo de fabricação. A detecção precoce pode ajudar a mitigar os problemas antes que eles se agravem.
Treinamento e Conscientização: Garantir que todo o pessoal envolvido no processo de fabricação de PCB seja treinado nas melhores práticas de laminação e usinagem. A consciência dos fatores que contribuem para a delaminação pode levar a uma melhor tomada de decisão.
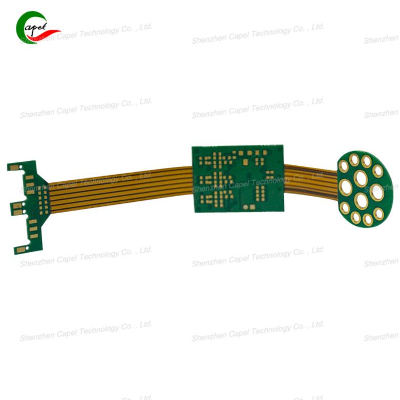
Horário da postagem: 31 de outubro de 2024
Voltar