6 dedos do ouro do PWB das placas de circuito do PWB FR4 da camada HDI
Capacidade de processo de PCB
Não. | Projeto | Indicadores técnicos |
1 | Camada | 1-60 (camada) |
2 | Área máxima de processamento | 545x622mm |
3 | Espessura mínima da placa | 4 (camada) 0,40 mm |
6 (camada) 0,60 mm | ||
8 (camada) 0,8 mm | ||
10 (camada) 1,0 mm | ||
4 | Largura mínima da linha | 0,0762 mm |
5 | Espaçamento mínimo | 0,0762 mm |
6 | Abertura mecânica mínima | 0,15 mm |
7 | Espessura de cobre da parede do furo | 0,015 mm |
8 | Tolerância de abertura metalizada | ±0,05mm |
9 | Tolerância de abertura não metalizada | ±0,025mm |
10 | Tolerância de furo | ±0,05mm |
11 | Tolerância dimensional | ±0,076 mm |
12 | Ponte mínima de solda | 0,08 mm |
13 | Resistência de isolamento | 1E+12Ω(normal) |
14 | Proporção de espessura da placa | 1:10 |
15 | Choque térmico | 288 ℃ (4 vezes em 10 segundos) |
16 | Distorcido e dobrado | ≤0,7% |
17 | Força anti-eletricidade | >1,3KV/mm |
18 | Força anti-decapagem | 1,4N/mm |
19 | A solda resiste à dureza | ≥6H |
20 | Retardador de chama | 94V-0 |
21 | Controle de impedância | ±5% |
Fazemos PCB HDI de 6 camadas com 15 anos de experiência com nosso profissionalismo
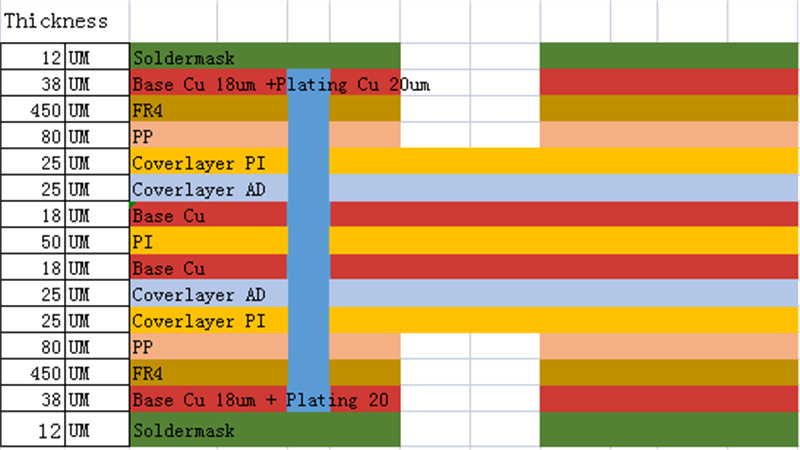
Placas Flex-Rígidas de 4 camadas
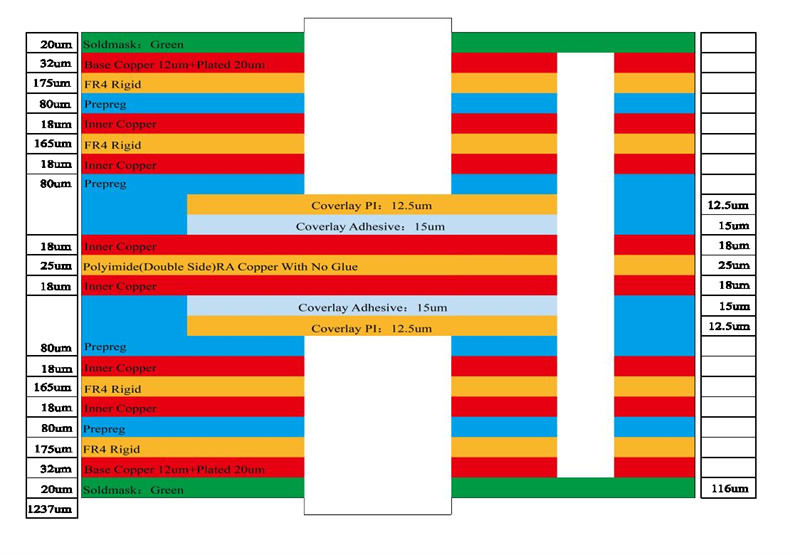
PCBs rígidos-flexíveis de 8 camadas
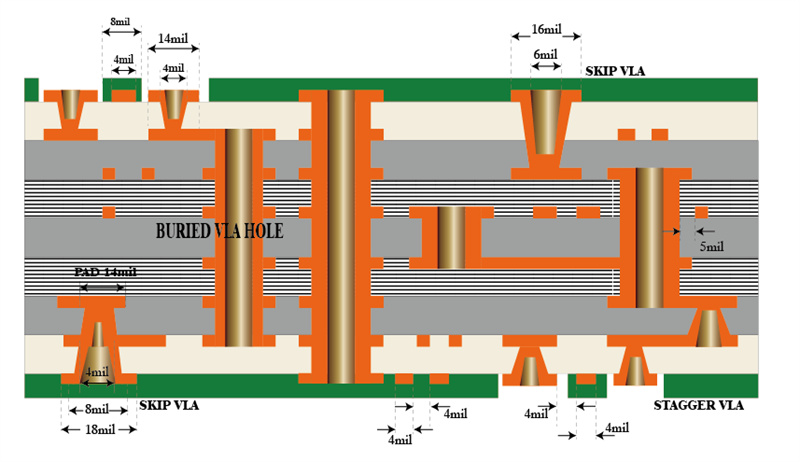
placas de circuito impresso HDI de 8 camadas
Equipamento de teste e inspeção
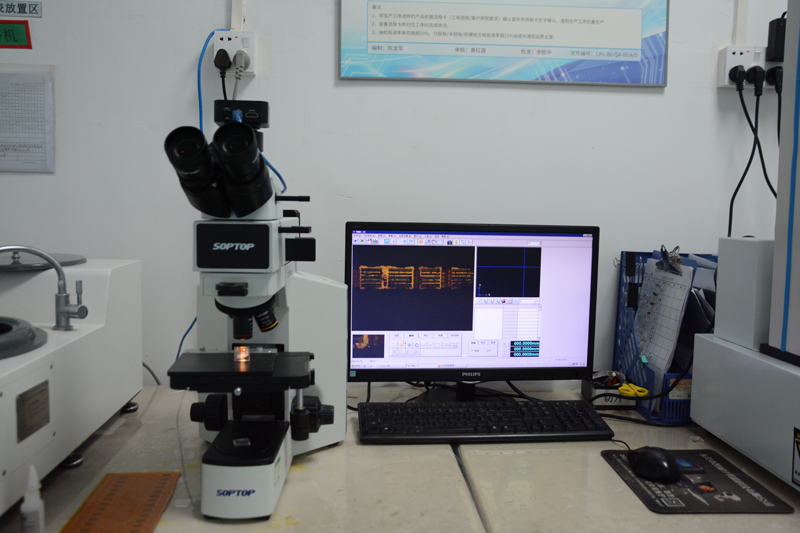
Teste de microscópio
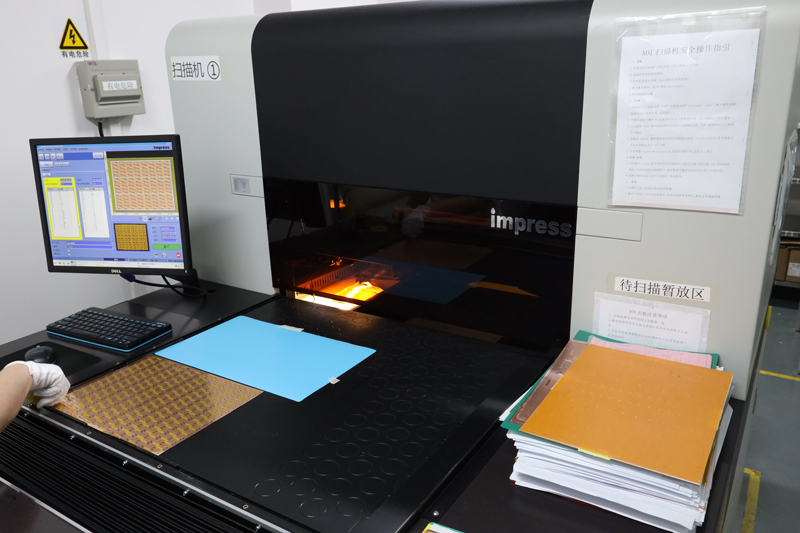
Inspeção AOI
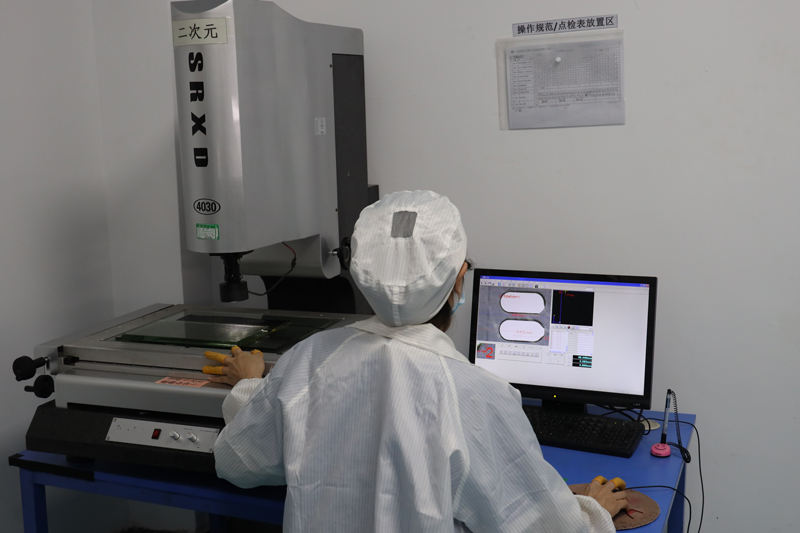
Teste 2D
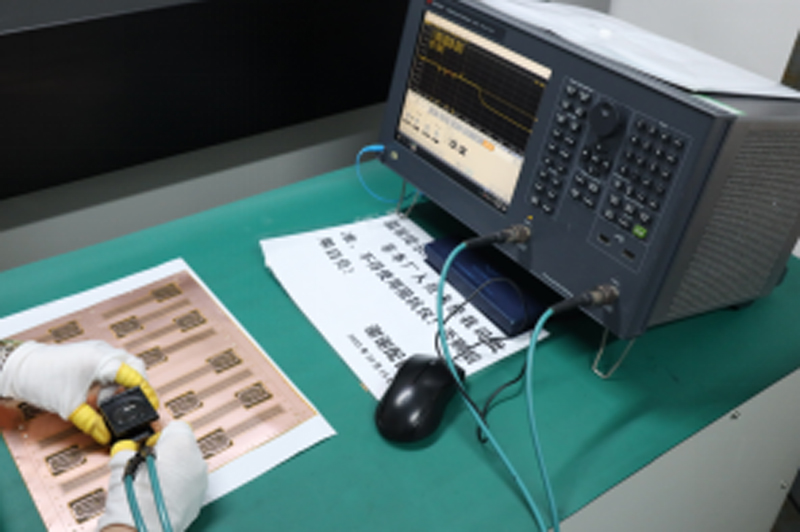
Teste de Impedância
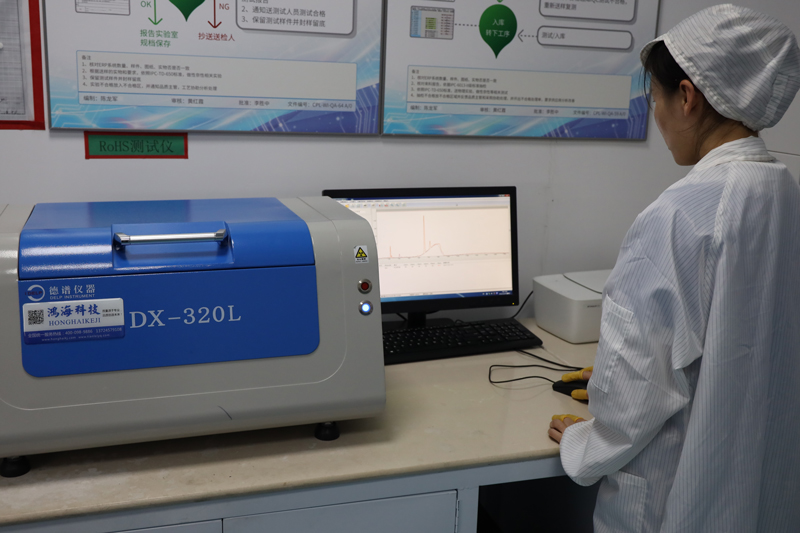
Teste RoHS
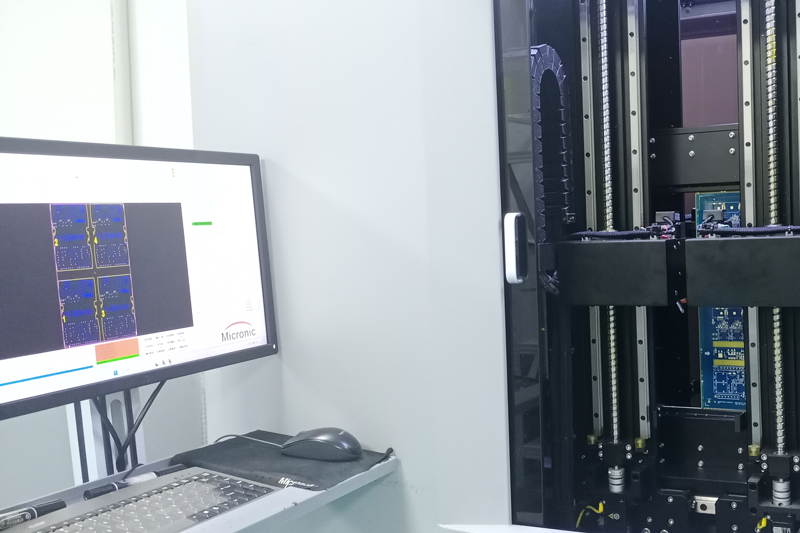
Sonda Voadora
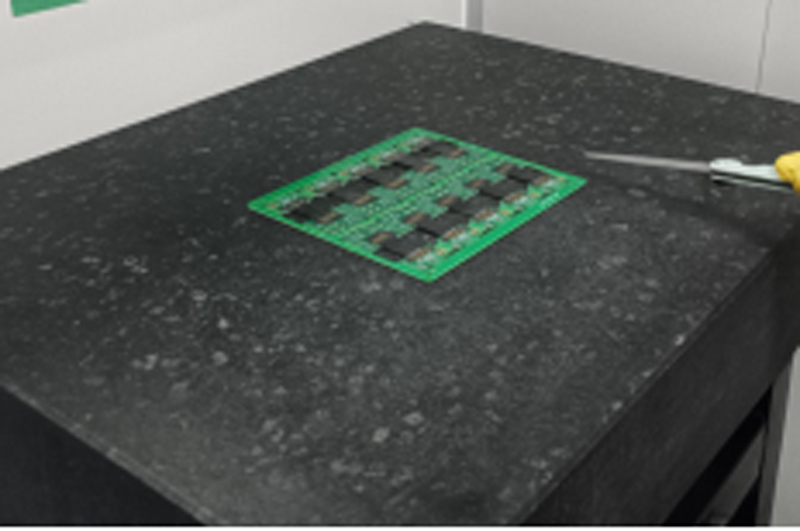
Testador horizontal
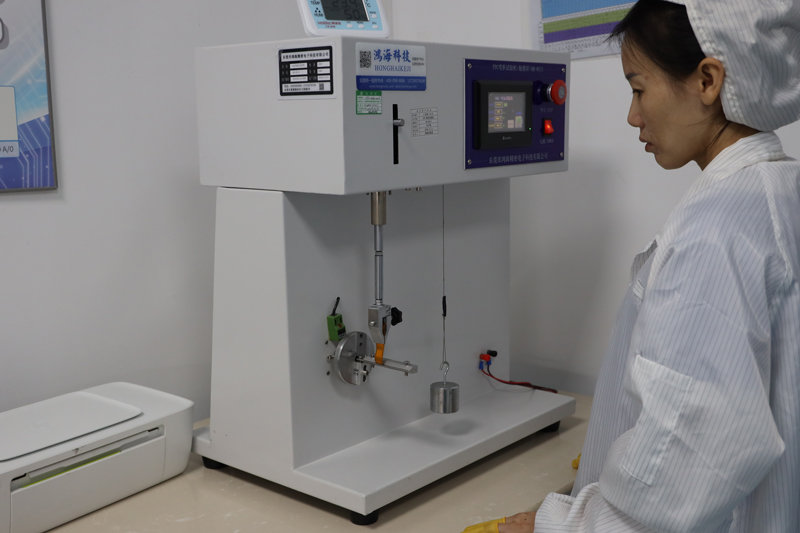
Teste de flexão
Nosso serviço HDI PCB de 6 camadas
. Fornecer suporte técnico Pré-venda e pós-venda;
. Personalizado até 40 camadas, 1-2 dias Prototipagem confiável de giro rápido, aquisição de componentes, montagem SMT;
. Atende dispositivos médicos, controle industrial, automotivo, aviação, eletrônicos de consumo, IOT, UAV, comunicações, etc.
. Nossas equipes de engenheiros e pesquisadores se dedicam a atender às suas necessidades com precisão e profissionalismo.
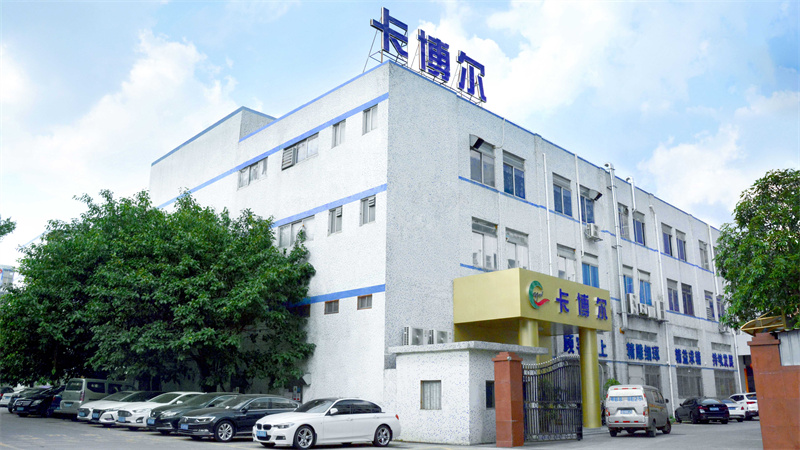
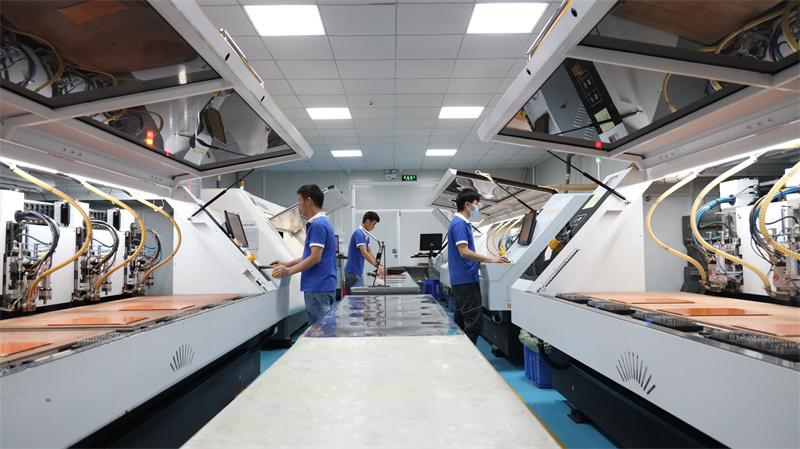
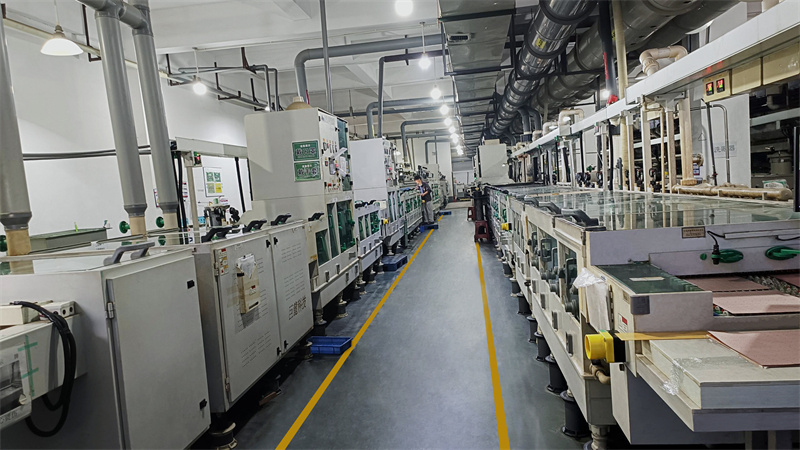
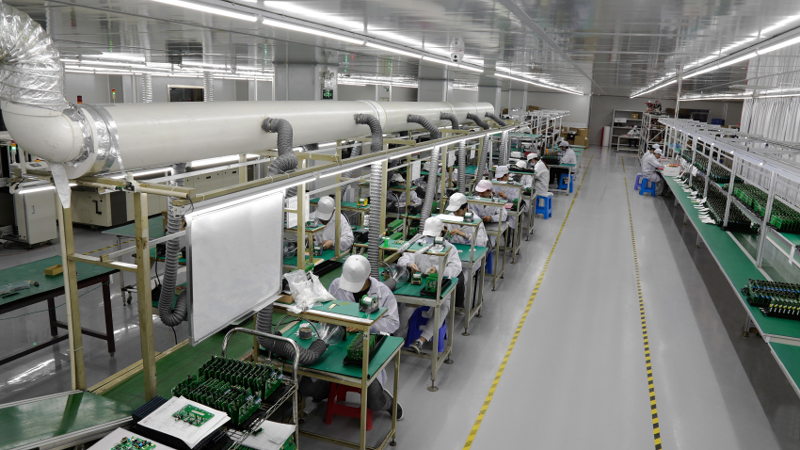
Aplicação específica de PCB HDI de 6 camadas no setor automotivo
1. ADAS (Sistema Avançado de Assistência ao Motorista): Os sistemas ADAS contam com vários sensores, como câmeras, radares e lidars, para ajudar os motoristas a navegar e evitar colisões. Um PCB HDI de 6 camadas é usado em módulos ADAS para acomodar conexões de sensores de alta densidade e garantir transmissão de sinal confiável para detecção precisa de objetos e alertas de driver.
2. Sistema de infoentretenimento: O sistema de infoentretenimento em veículos modernos integra diversas funções, como navegação GPS, reprodução de multimídia, opções de conectividade e interfaces de comunicação. A PCB HDI de 6 camadas permite a integração compacta de componentes, conectores e interfaces, garantindo comunicação eficiente, controle confiável e experiência de usuário aprimorada.
3. Unidade de Controle do Motor (ECU): A unidade de controle do motor é responsável por monitorar e controlar várias funções do motor, como injeção de combustível, ponto de ignição e controle de emissões. A PCB HDI de 6 camadas ajuda a acomodar circuitos complexos e comunicação de alta velocidade entre diferentes sensores e atuadores do motor, garantindo controle preciso e eficiência do motor.
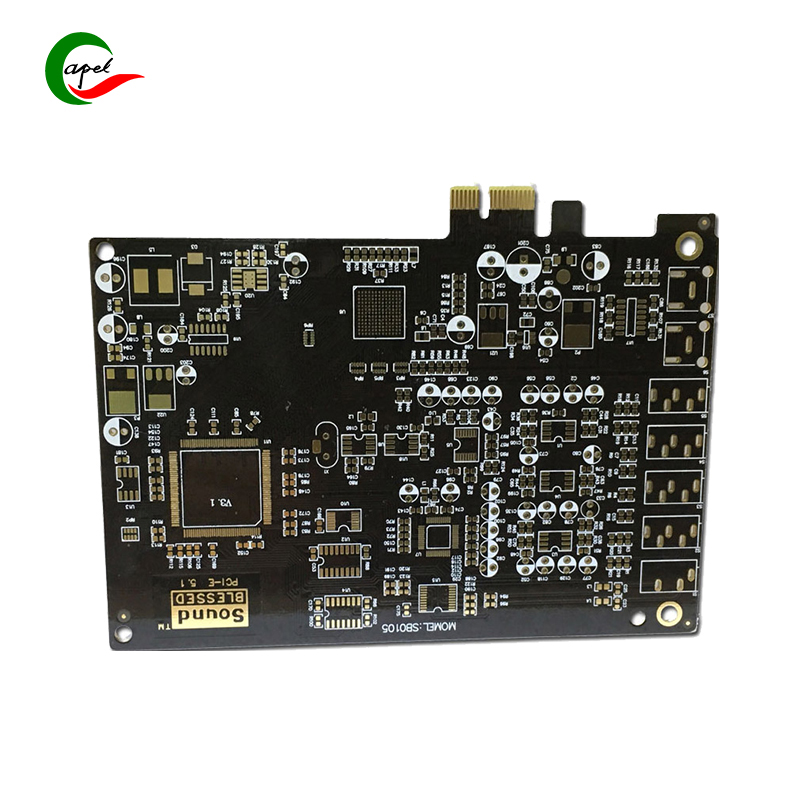
4. Controle Eletrônico de Estabilidade (ESC): O sistema ESC melhora a estabilidade e a segurança do veículo monitorando e ajustando continuamente a frenagem individual das rodas e o torque do motor. O HDI PCB de 6 camadas desempenha um papel vital no módulo ESC, facilitando a integração de microcontroladores, sensores e atuadores para análise de dados em tempo real e controle preciso.
5. Trem de força: A unidade de controle do trem de força (PCU) regula a operação do motor, da transmissão e do trem de força para desempenho e eficiência ideais. O HDI PCB de 6 camadas integra vários componentes de gerenciamento de energia, sensores de temperatura e interfaces de comunicação, garantindo transferência de energia eficiente, troca de dados confiável e gerenciamento térmico eficaz.
6. Sistema de gerenciamento de bateria (BMS): O BMS é responsável por monitorar e controlar o desempenho, carregamento e proteção da bateria do veículo. O PCB HDI de 6 camadas permite design compacto e integração de componentes BMS, incluindo ICs de monitoramento de bateria, sensores de temperatura, sensores de corrente e interfaces de comunicação, garantindo gerenciamento preciso da bateria e prolongando a vida útil da bateria.
Como o PCB HDI de 6 camadas melhora a tecnologia no setor automotivo?
1. Miniaturização: PCB HDI de 6 camadas permite a colocação de componentes de alta densidade, realizando assim a miniaturização de sistemas eletrônicos. Isto é fundamental na indústria automotiva, onde o espaço é frequentemente limitado. Ao reduzir o tamanho do PCB, os fabricantes podem projetar veículos menores, mais leves e mais compactos.
2. Melhorar a integridade do sinal: a tecnologia HDI reduz o comprimento dos traços de sinal e fornece melhor controle de impedância.
Isto melhora a qualidade do sinal, reduz o ruído e melhora a integridade do sinal. Garantir um desempenho confiável do sinal é fundamental em aplicações automotivas onde a transmissão e a comunicação de dados são essenciais.
3. Funcionalidade aprimorada: Camadas adicionais em uma PCB HDI de 6 camadas fornecem mais espaço de roteamento e opções de interconexão, permitindo funcionalidade aprimorada. Os carros agora integram uma variedade de funções eletrônicas, como sistemas avançados de assistência ao motorista (ADAS), sistemas de infoentretenimento e unidades de controle do motor. O uso de HDI PCB de 6 camadas facilita a integração dessas funções complexas.
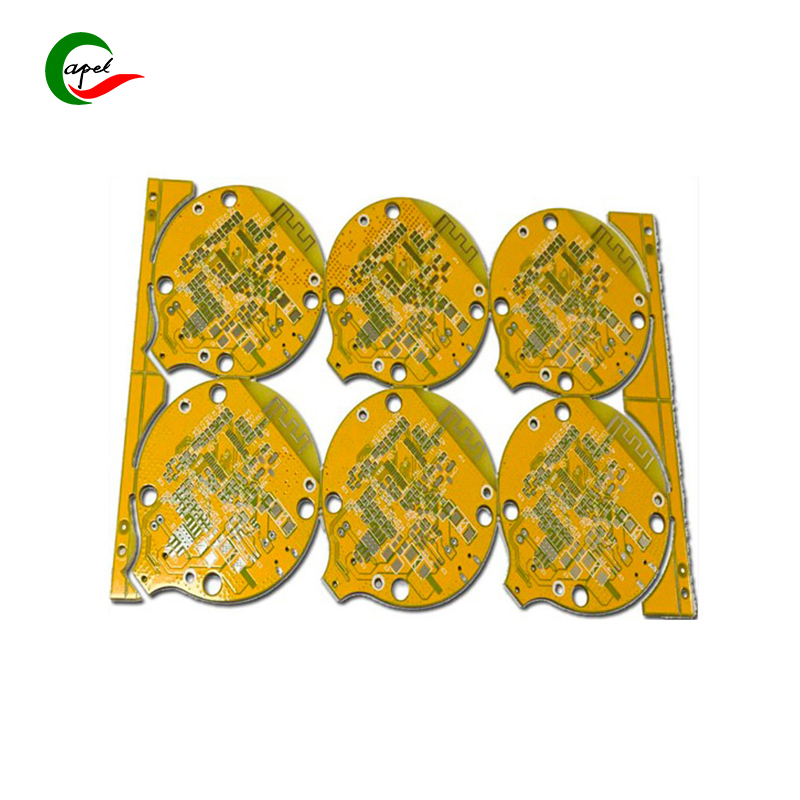
4. Transmissão de dados em alta velocidade: Os sistemas automotivos, como sistemas avançados de navegação e comunicação entre veículos, exigem transmissão de dados em alta velocidade. O HDI PCB de 6 camadas suporta aplicações de alta frequência para transmissão de dados mais rápida e eficiente. Isto é fundamental para a tomada de decisões em tempo real, melhorando a segurança e o desempenho.
5. Confiabilidade aprimorada: a tecnologia HDI utiliza microvias para fornecer melhores conexões elétricas enquanto ocupa menos espaço.
Essas vias menores ajudam a melhorar a confiabilidade, reduzindo o risco de interferência de sinal e incompatibilidade de impedância. Na eletrônica automotiva, onde a confiabilidade é crítica, os PCBs HDI garantem conexões robustas e duráveis.
6. Gerenciamento térmico: Com a crescente complexidade e consumo de energia da eletrônica automotiva, o gerenciamento térmico eficiente é fundamental. O PCB HDI de 6 camadas suporta a implementação de vias térmicas para ajudar a dissipar o calor e regular a temperatura.
Isto permite que os sistemas automotivos operem de forma ideal, mesmo em altas temperaturas.